Alfa Laval Bactofuge Separator
The use of bactofuge centrifugal separators is an important tool for improving the quality and safety of dairy products, and is a standard practice in many dairy processing plants. Bactofuge separators use centrifugal force to separate bacteria from the milk or dairy product, which is then removed from the separator as a concentrated “sludge” or “cake”.
The process typically begins with the milk being fed into the bactofuge separator, where it is accelerated to high speeds by a rapidly rotating drum or bowl. As the milk or dairy product is subjected to these high speeds, centrifugal force causes the denser components to move outward towards the walls of the drum, while the less dense components, such as milk or cream, remain in the center.
The sludge is then removed from the product by opening a valve at the bottom, which allows it to be removed from the system.
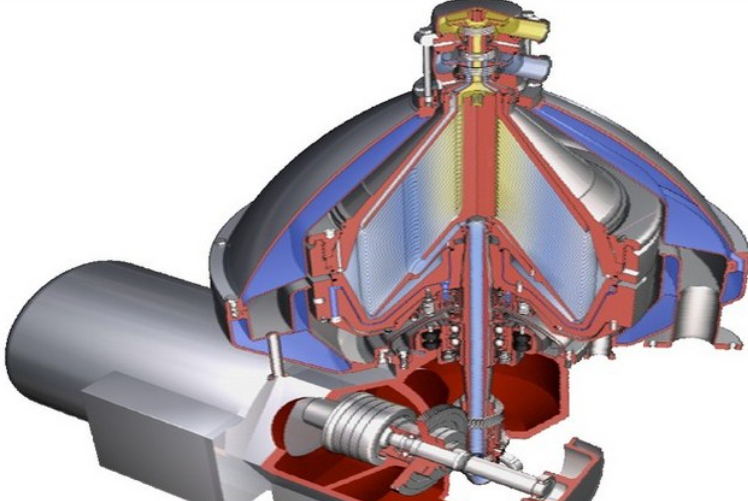
General Overview
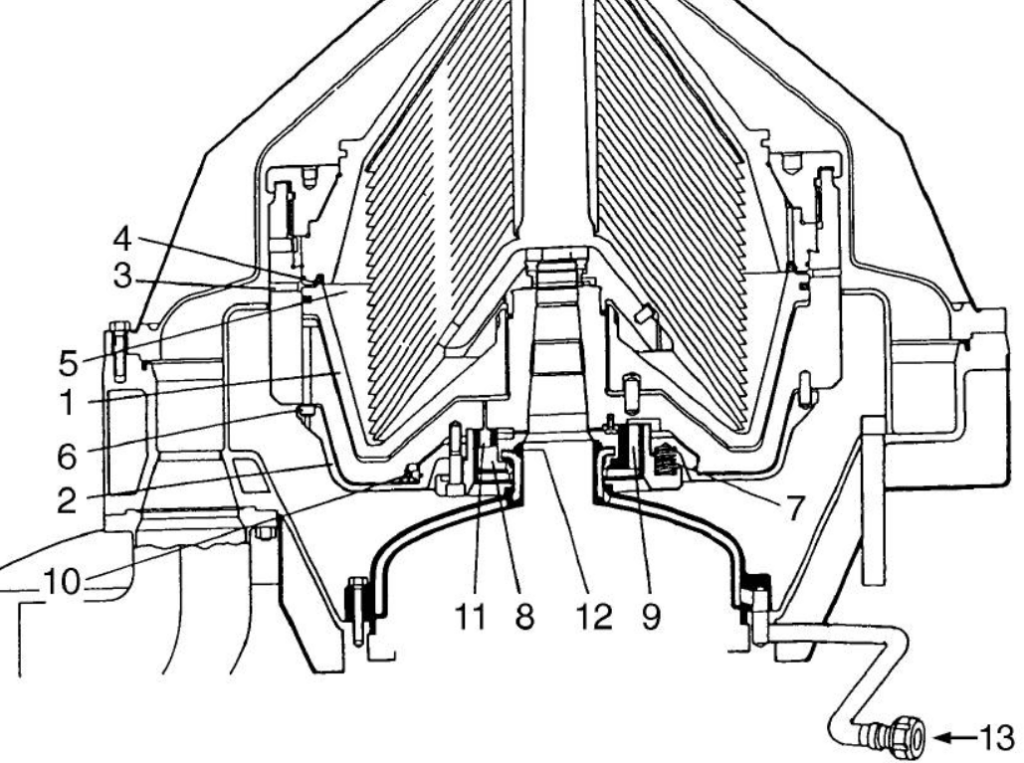
Bowl
1.Sliding bowl bottom
2.Operating slide
3.Sediment ports
4.Seal ring
5.Sediment space
6.Valve plugs
7.Coil springs
8.Closing water chamber
9.Opening water channel(discharge)
10. Draining nozzle
11. Closing water channel
12. Control paring disc
13. Operating water supply from the OWMC
Operation
The bowl wall of the separator has three ports through which sediment discharge occurs. When the ports are closed, the sliding bowl bottom acts as an internal bottom in the separating space and is held against a seal ring by the water pressure acting on its underside. The pressure is generated during the bowl’s rotation due to centrifugal force and increases as the distance from the axis of rotation of the bowl increases. The operating water generates an upward pressure that exceeds the downward pressure from the process liquid because the underside of the sliding bowl bottom has a larger pressure surface area than its upper side.
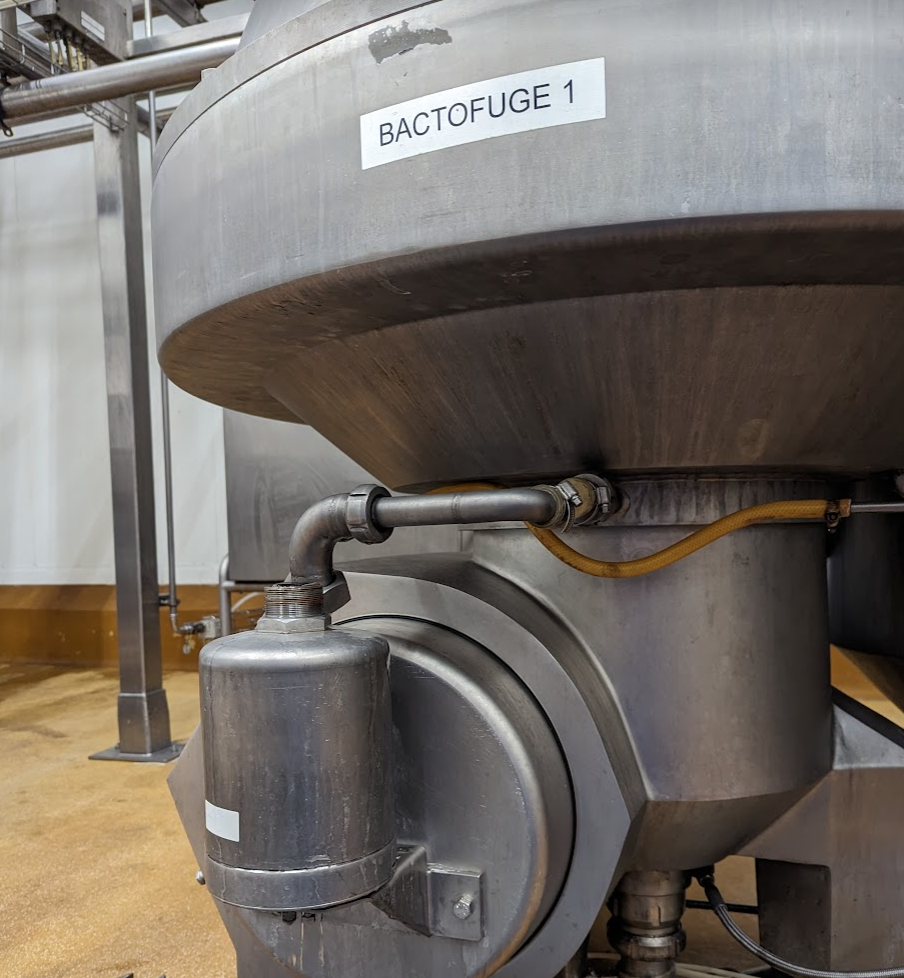
The space beneath the sliding bowl bottom is kept closed by valve plugs that are seated in an operating slide. The slide is forced upwards by coil springs, and a constant water level is maintained in the operating water chamber using a paring disc.
- To initiate a discharge, compressed air is used to force the piston in the OWMC forward.
- Water is supplied in a sufficient quantity so that it flows over the edge of the operating water chamber and onwards through the channel to the upper side of the operating slide.
- The slide is forced downwards by the liquid pressure created between the operating slide and the bowl body, thereby opening the valve plugs that enable the closing water under the sliding bowl bottom to escape.
- The sliding bowl bottom is pressed downwards, uncovering the ports in the bowl wall so that the sediment is discharged.
- The water on the upper side of the operating slide is drained off through a nozzle.
- When water has been sufficiently drained through the nozzle, the coil springs again force the operating slide upwards, closing the valve plugs. The sliding bowl bottom is forced upwards by the operating water supply, thus closing the bowl.
- Low-pressure water is supplied during the whole cycle.
- The operating water now presses the OWMC piston back into its end position by means of the operating water pressure, and the discharge is completed.
- Solids and/or excessive mineral content in the operating water will disturb, and eventually block the discharge function.
Discharges
There are two sediment discharge volumes available for emptying solids from the separator bowl, which are determined by the duration of the increased flow of operating liquid from the Operating Water Module Compact (OWMC) while the bowl is open. The discharge volumes can be classified as either small or large, depending on the duration of the increased flow of operating liquid.
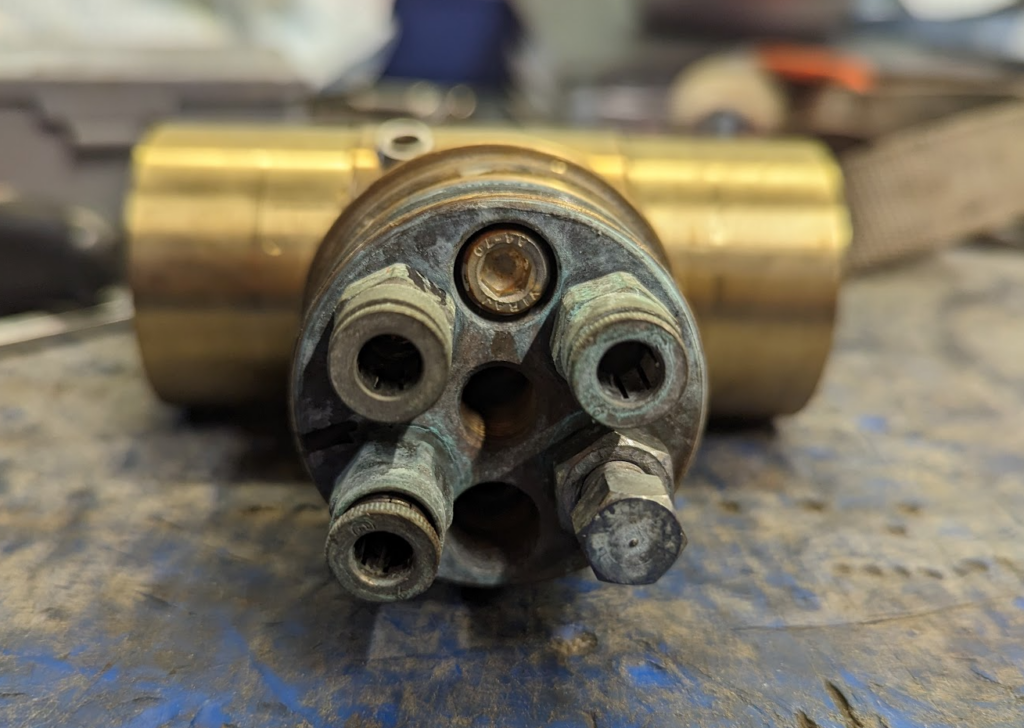
Starting from the top left, we have the main air supply that should be between 4-6 bar. Top right is a control signal for the big discharge. Left bottom is the control signal for the small discharge.
Disassmebly of the OWMC
The OWMC is designed as a stainless steelconstruction consisting of an air reservoir (6), awater cylinder (3) with piston (4) and a servovalve (5). The module is equipped withconnections for air supply (506a) and signal air(506b and c).The OWMC is also equipped with a needle valve(8) for regulating of air flow for the smalldischarge and a silencer (7).
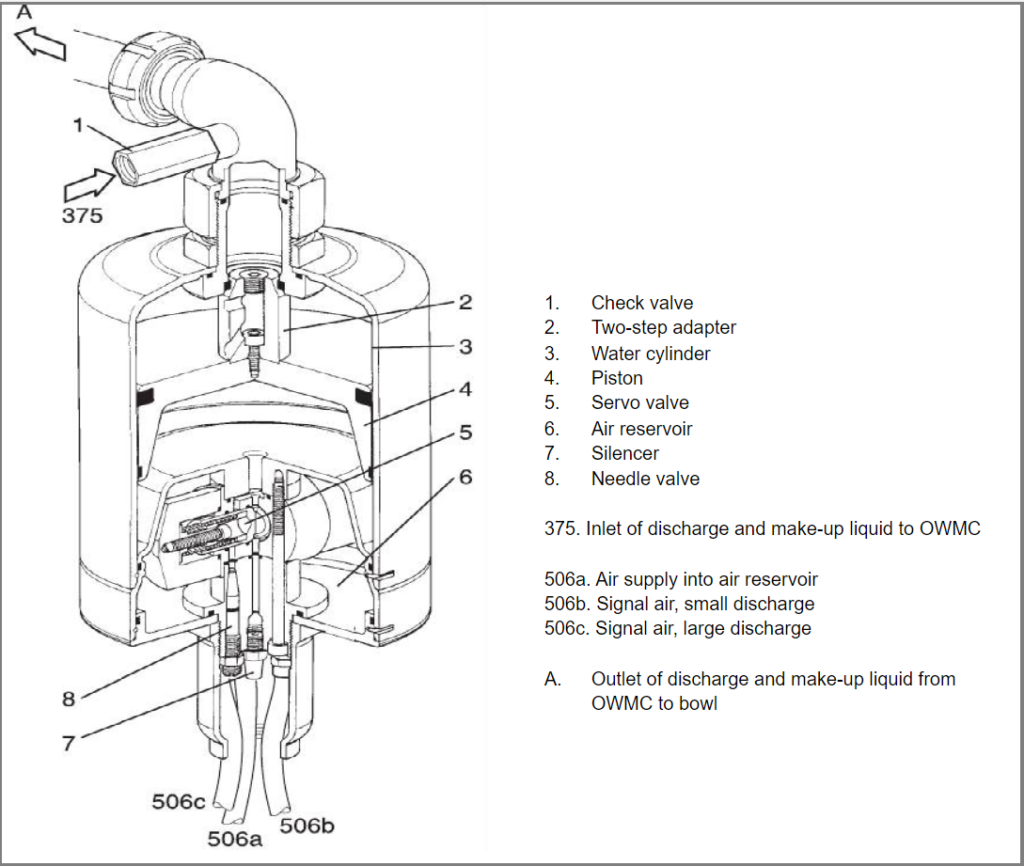
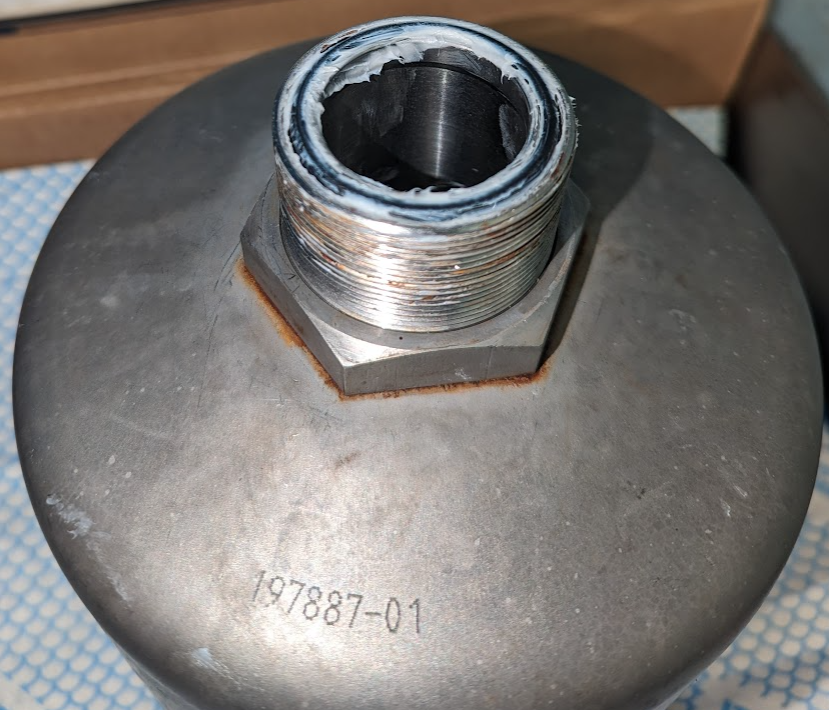
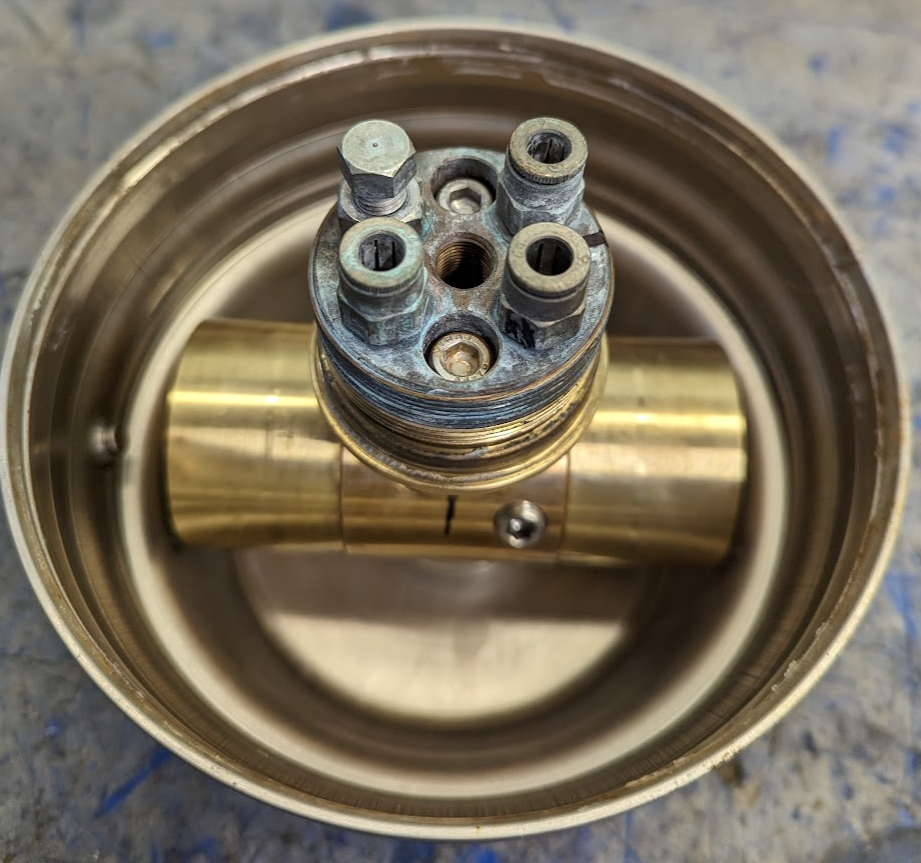
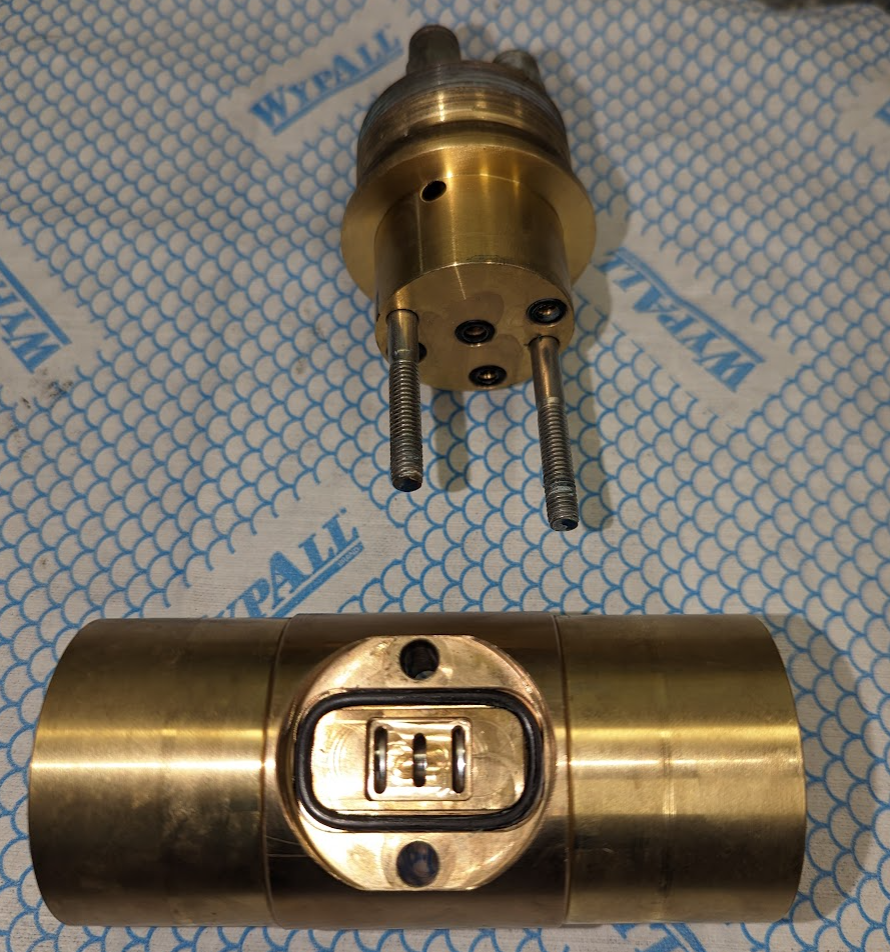
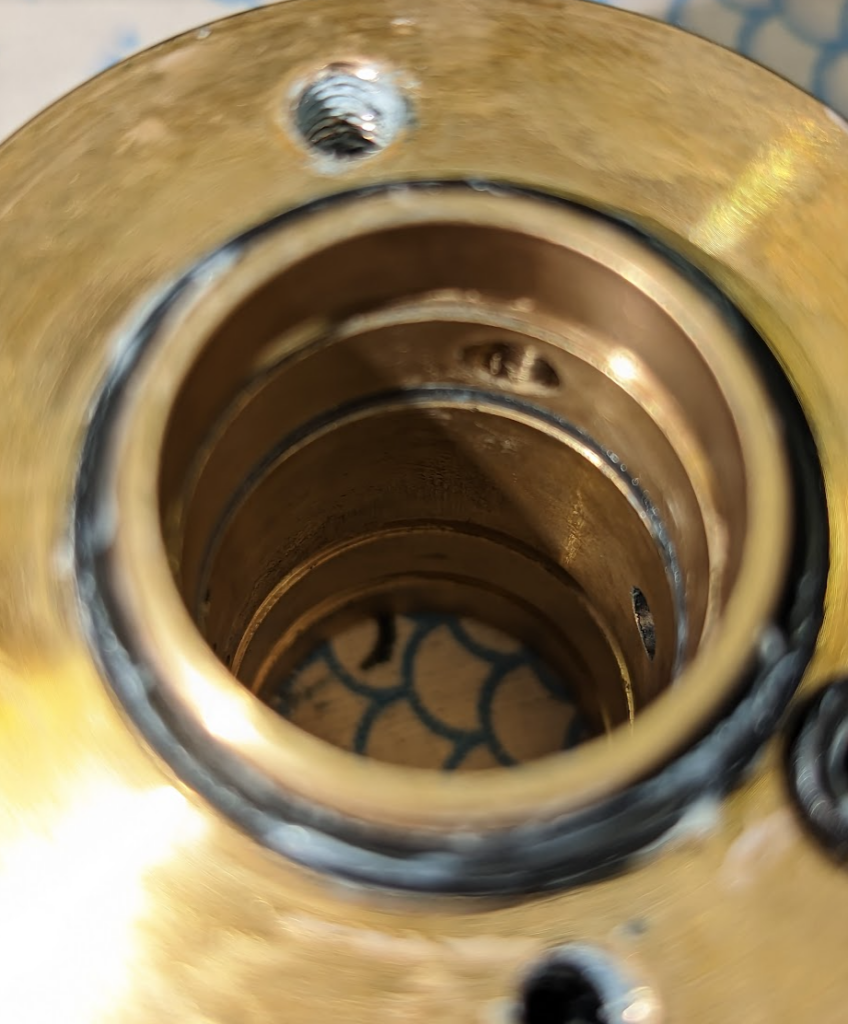
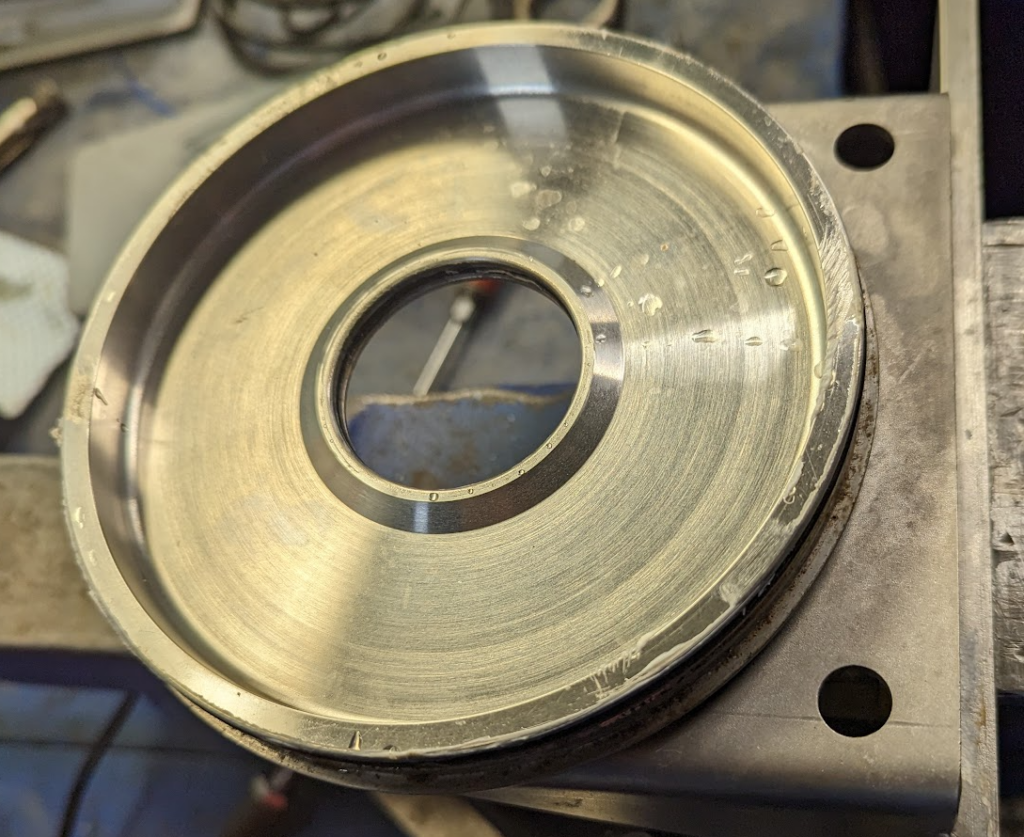
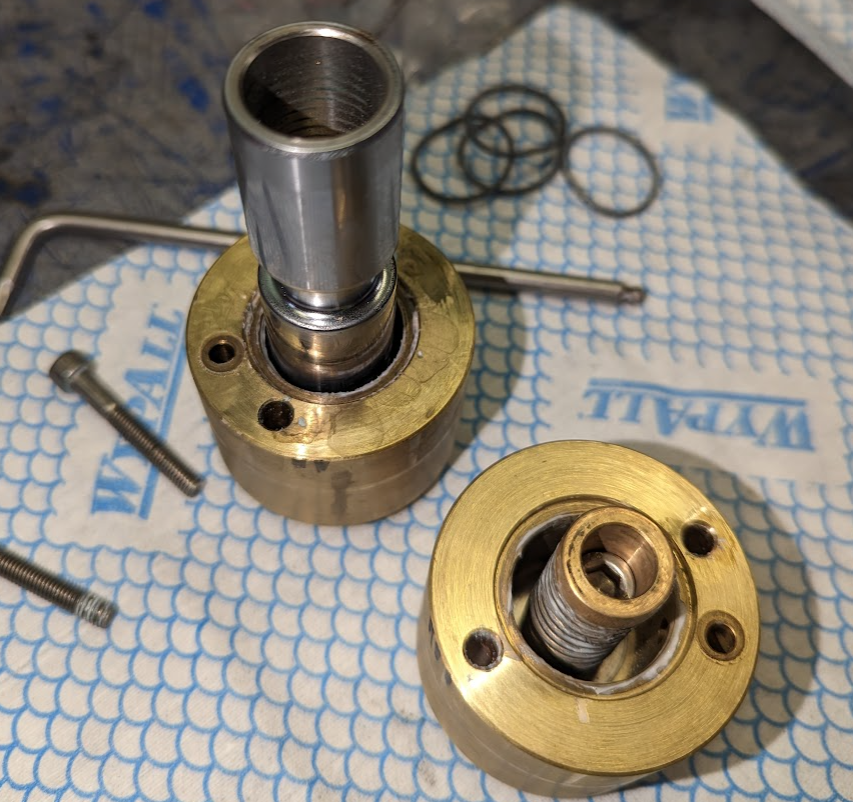
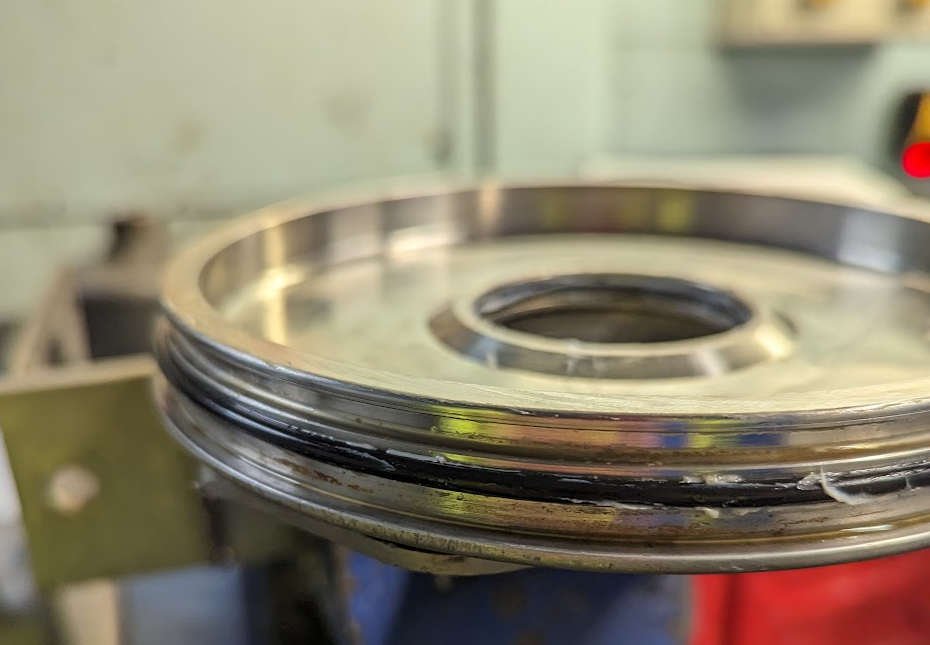
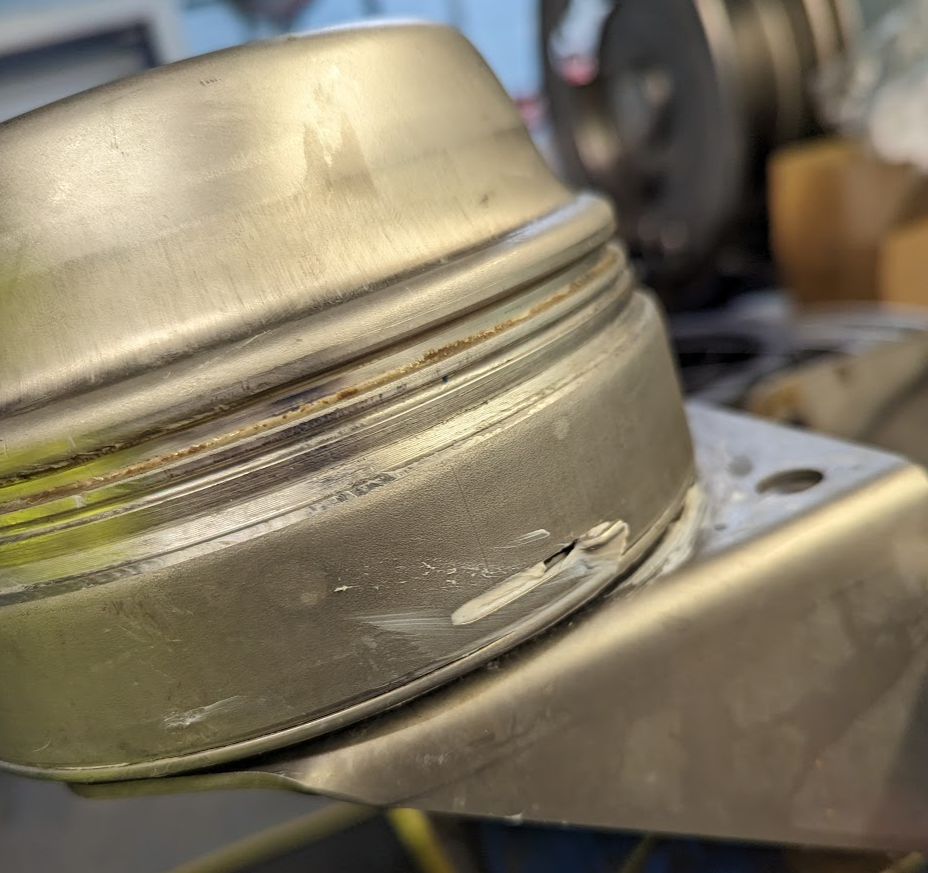
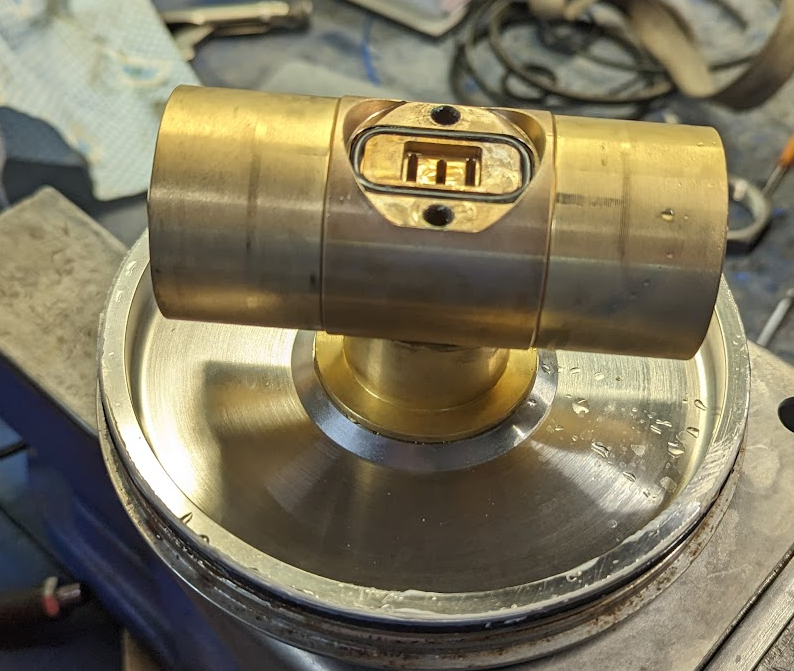
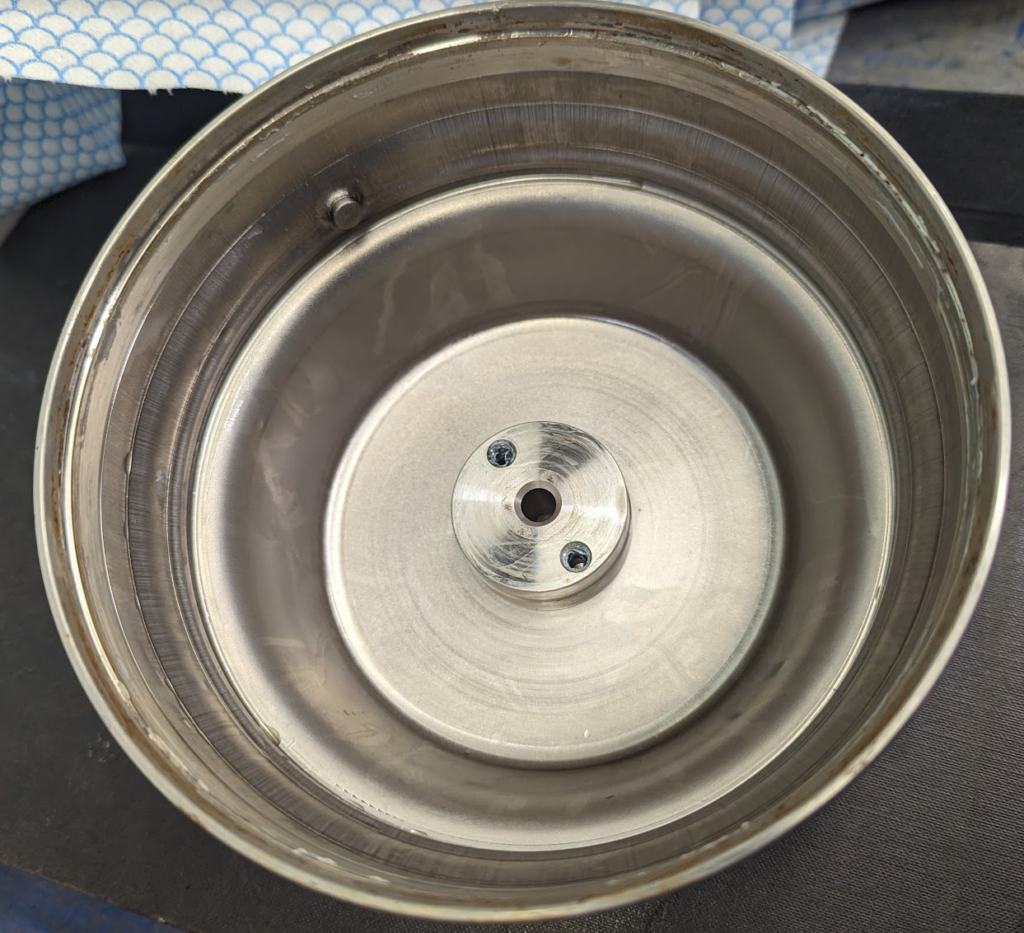
Preventive Maintenance
The OWMC (Operating Water Module Compact) is an essential component of the centrifugal separator system. It is responsible for regulating the flow of water that is used to control the pressure inside the separator bowl, which is critical for separating the solids from the liquid.
If the OWMC is not functioning properly, it can affect the performance of the entire centrifugal separator system, leading to issues such as incomplete separation of solids, reduced efficiency, increased energy consumption, and even damage to the separator equipment. Therefore, it is important to perform regular maintenance and servicing of the OWMC to ensure its proper functioning and to prevent any potential issues that could affect the overall performance of the centrifugal separator system.